Understanding CNC Machine Time Cost: Key Factors
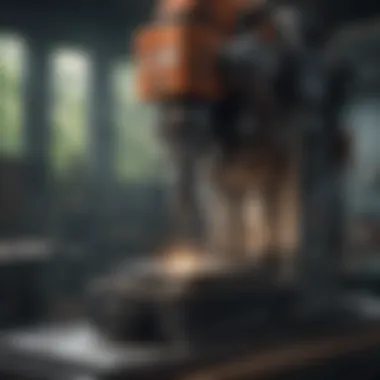
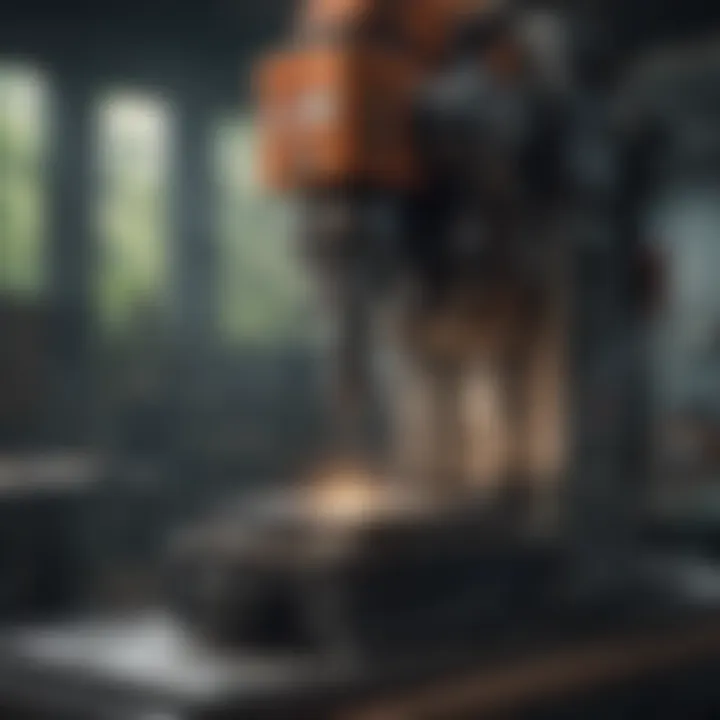
Intro
CNC machining represents a pivotal technology in modern manufacturing. Understanding the cost per hour is essential for businesses aiming to optimize their budgets and enhance profitability. This cost encompasses various elements, each influencing the overall expenditure. In this article, we will dissect these elements, from machine types to labor rates, elucidating how they impact the hourly cost of CNC machining. By doing so, we aim to provide insights for industry professionals seeking to make informed decisions.
Factors Influencing CNC Machine Time Cost Per Hour
Machine Type
Different CNC machines vary significantly in cost and efficiency. For instance, a Haas VF-2 is designed for compact machining but has limited capabilities compared to larger models like the Mazak VTC-760. Choosing the right machine type is crucial as it dictates not only the purchase price but also the operational cost over time. The complexity of each machine’s function can lead to different machining speeds, which in turn affects the cost per hour of operation.
Operational Efficiencies
Operational efficiency is a critical component of CNC machining economics. Factors such as setup time, feed rates, and tool wear play considerable roles in determining overall efficiency. High inefficiencies can lead to increased operational costs. For example, if a machine is idle due to improper setup, the costs incurred during that time accumulate, increasing the effective hourly rate.
Key aspects of operational efficiencies include:
- Minimizing setup time.
- Maintaining optimal feed rates.
- Monitoring tool wear to prevent unplanned downtimes.
Material Costs
The choice of materials significantly impacts the CNC machine time cost per hour. Premium materials like titanium are more expensive than aluminum or plastic. Furthermore, the machining of tougher materials typically requires more time and specialized tools. Thus, the material choice directly affects labor and equipment usage, leading to a variation in operational costs.
Labor Rates
Human labor remains a hefty component of CNC time costs. Labor rates differ by region, experience, and the specific skills required for high-tech CNC operations. A skilled technician not only operates the machinery but also performs quality checks, which adds to the cost per hour. Companies must factor these rates into their budget calculations.
Maintenance Needs
Regular maintenance is vital for CNC machines to function efficiently. Unscheduled downtimes due to machine failure can severely inflate costs. Knowing the machine's maintenance schedule and budgeting for it helps in planning operational costs effectively. Businesses need to invest not only in upfront costs but also in ongoing maintenance expenses to ensure long-term profitability.
Technological Advancements
Staying abreast of technological advancements can also influence CNC machining costs. Newer machines often come with built-in efficiencies and automation features that can reduce labor and material costs. Investing in the latest technologies may require a higher initial financial outlay, but it can lead to significant savings and productivity improvements in the long run.
"Investing in advanced CNC technologies is not just about current capabilities; it is about future-proofing your operations against evolving market demands."
The End
Foreword to CNC Machining
The world of CNC machining plays a vital role in modern manufacturing. Understanding CNC machining is not just about knowing how the machines operate. It also involves grasping the economic implications behind their use. The discussion on CNC machining costs can influence decisions at various levels. Any business or individual involved in production must acknowledge the expense associated with time on CNC machines. Evaluating costs accurately can significantly impact the bottom line.
Definition and Overview
CNC, which stands for Computer Numerical Control, refers to the automated control of machining tools. This control is based on computer input, producing precise and repeatable results. CNC machines can manufacture parts and components in various industries, including aerospace, automotive, and electronics. Common machines include lathes, mills, routers, and plasma cutters. With CNC technology, tasks that require significant manual effort can be completed with increased accuracy and speed. This leads to higher productivity and less waste in manufacturing processes.
Importance in Manufacturing
The importance of CNC machining in manufacturing cannot be overstated. First, it allows for high precision in creating parts. Accurate dimensions are essential, especially in industries that require tight tolerances. Secondly, the efficiency gained from CNC machines translates to lower labor costs. As machines can operate continuously, less manual labor is often needed, freeing skilled workers for other tasks. Moreover, CNC machining enables complex designs to be manufactured with relative ease. This capability allows designers to push the boundaries of what can be produced.
"CNC technology is crucial for maintaining competitive advantages in manufacturing."
In summary, CNC machining is a cornerstone of modern production environments. Its understanding helps to decipher various cost elements involved, fundamentally impacting economic planning and operational strategies.
Understanding Cost Components
In any CNC machining project, understanding cost components is crucial for effective budgeting and project management. This section focuses on dissecting both direct and indirect costs as well as the distinction between variable and fixed costs. Mastery of these elements helps professionals predict expenditures accurately, ensuring that projects remain financially viable.
Direct and Indirect Costs
Direct costs are expenses that can be directly attributed to the production of CNC machined parts. These include materials like metals, plastics, and other raw inputs. Furthermore, it encompasses labor costs for the workers directly involved in the machining process. Understanding these costs enables companies to effectively gauge pricing and profit margins.
On the other hand, indirect costs are those not directly tied to a specific product but crucial for overall operations. Examples include utilities, rent, and administrative salaries. These costs often go unnoticed but can significantly impact the overall budget. Awareness of direct and indirect costs is essential for forming a comprehensive financial picture for CNC operations.
Variable versus Fixed Costs
Variable costs fluctuate based on production output. For instance, as production volume increases, the costs associated with materials and labor may vary correspondingly. Analyzing variable costs allows companies to discover economies of scale and optimize spending based on production quantities. This adaptability is vital for managing finances efficiently, especially in fluctuating markets.
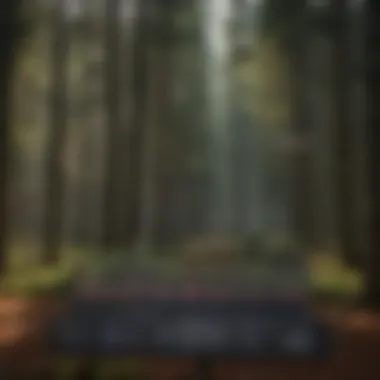
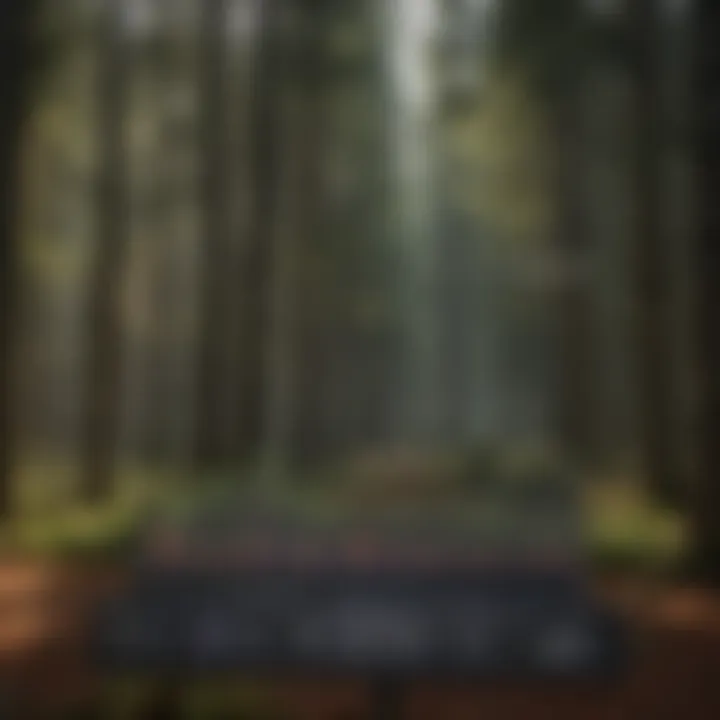
In contrast, fixed costs remain constant regardless of production levels. These include lease payments and salaries of machine operators. Even in periods of low production, fixed costs do not change, making them less flexible in terms of budget adjustments. Understanding the balance between variable and fixed costs is important. It informs financial strategies and facilitates more accurate forecasting of CNC operations.
"A keen understanding of cost components enhances decision-making capabilities for any CNC project."
Factors Influencing CNC Time Cost
Understanding the factors that influence CNC time cost is essential for both industry professionals and those looking to optimize their operations. Each element contributes to the overall expenses associated with CNC machining, which can significantly impact profitability. An in-depth analysis helps identify areas for improvement and cost reduction. This section delves into three main factors: machine type and specifications, material selection, and production volume.
Machine Type and Specifications
The type of CNC machine used plays a crucial role in dictating hourly costs. Different machines serve specific functions, and their capabilities directly influence their operational cost. For instance, a high-end five-axis CNC machine typically incurs a higher hourly rate compared to a standard three-axis model due to its increased capabilities and complexity.
Key points to consider include:
- Complexity of Operations: Machines that can perform intricate tasks require more sophisticated technology, leading to higher costs.
- Power Consumption: Larger machines with higher specifications will consume more energy, translating to increased operational costs.
- Maintenance Requirements: High-precision machines often need more routine and unscheduled maintenance, affecting the cost per hour of operation.
Material Selection
Choosing the right material also significantly impacts the time cost of CNC machining. Different materials have varying properties, machinability, and costs associated with them. For instance, metals like titanium are much harder to machine than aluminum, resulting in longer machining times and higher wear on tools.
Factors to consider in material selection include:
- Machinability: The ease with which a material can be cut affects cycle times. Materials that are easier to machine will reduce overall costs.
- Material Costs: Higher-priced materials will naturally raise the overall production cost. This requires careful budgeting and forecasting.
- Tooling: Certain materials may require specialized tooling that can increase initial investments but may result in long-term savings through efficiency.
Production Volume
Production volume directly correlates with CNC time costs. In higher volume production, fixed costs can be distributed over a larger number of units, leading to lower costs per piece. Conversely, lower volumes can result in disproportionately high costs.
When considering production volume, keep in mind:
- Setup Times: Each new job may incur setup times that add to the overall cost. Efficient setup processes can minimize this factor.
- Batch Processing: Producing in batches rather than one-off runs can enhance operational efficiency. It reduces wasted time and machinery idle rates, thus optimizing time cost.
- Economies of Scale: High-volume machining often leads to negotiated material costs and better use of machining capabilities per hour.
A comprehensive understanding of these factors allows CNC operators to anticipate and manage costs effectively, thus enhancing overall business sustainability.
Effective management of CNC machining costs requires careful attention to these influencing factors. By evaluating machine types, selecting materials judiciously, and optimizing production volume, professionals can ensure their operations remain competitive in an ever-evolving market.
Operational Efficiencies
Operational efficiencies in CNC machining are crucial to understanding the overall time cost per hour. These efficiencies relate to how well a facility utilizes its resources, including machinery, labor, and time. Optimizing these elements can lead to significant cost savings, increased production rates, and improved product quality. For CNC machining, where precision is key, even small improvements can have substantial financial impacts.
Setup Time and Its Impact
Setup time refers to the time taken to prepare a CNC machine for a new job. It includes tasks like loading the material, configuring the machine settings, and calibrating tools. Reducing setup time can vastly improve the cost-effectiveness of CNC operations. When setup time is minimized, machines spend more time actually cutting parts rather than being idle.
Some effective strategies to reduce setup time include:
- Standardization: Use standardized tools and fixtures to streamline the setup process.
- Pre-setup Preparation: Preparing tools and materials before the machine is turned off can save time in the next cycle.
- Operator Training: Skilled operators can perform setups more efficiently, reducing the time needed for this phase.
Downtime Analysis
Downtime refers to the periods when a CNC machine is not operational due to maintenance, repairs, or waiting for materials. Analyzing downtime is essential in reducing the overall cost per hour. When a machine is down, it is not contributing to production, which directly affects profitability.
A few methods for gap analysis include:
- Tracking Events: Use software to monitor and record downtime events to identify common issues.
- Root Cause Analysis: Identify the underlying causes of downtime to develop targeted solutions.
- Preventive Maintenance: Regular maintenance checks can prevent unscheduled downtimes.
By regularly analyzing downtime, companies can make informed decisions to optimize machine usage and ultimately drive down costs.
Cycle Times and Their Relevance
Cycle time measures the total time required to complete one production run or job. This includes machining time, part handling, and any other operational activities involved from start to finish. Understanding and optimizing cycle times is vital because they directly correlate with production efficiency and costs.
Some approaches to improve cycle times are:
- Automation: Employing automatic bar loaders or robotic arms can reduce handling time and errors.
- Tool Utilization: Using high-speed tooling can reduce machining times without sacrificing quality.
- Process Optimization: Regular review of operations to find bottlenecks allows for targeted improvements.
"A well-optimized cycle time can yield greater throughput and significantly lower the CNC machining cost per hour."
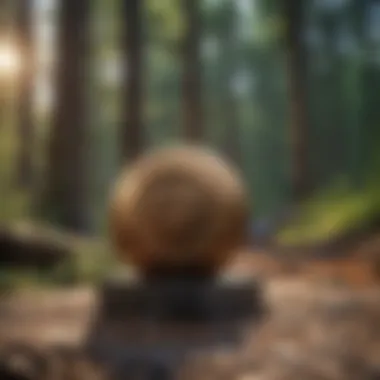
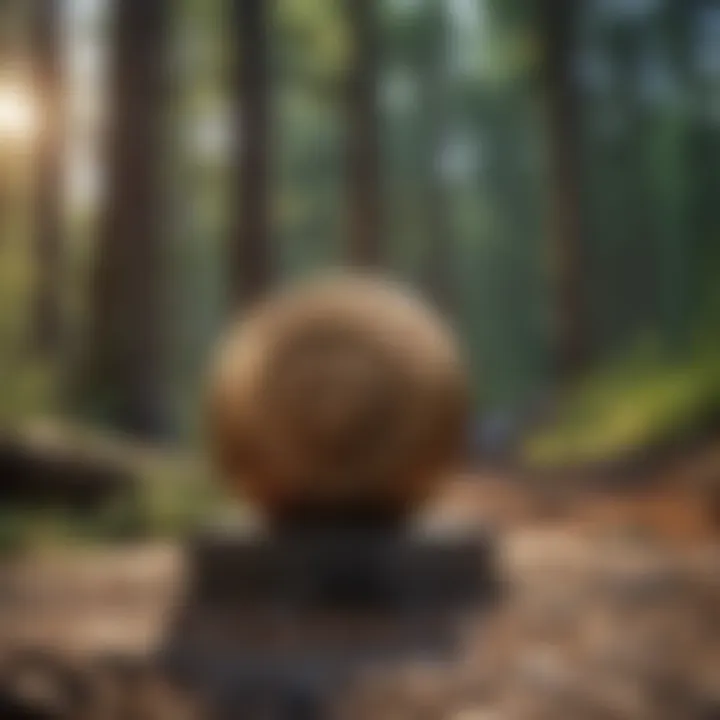
Labor Costs in CNC Machining
Labor costs play a pivotal role in determining the overall expenses associated with CNC machining. These costs are not merely a function of hourly wages; they also encompass various associated expenses, including benefits, taxes, and training. Understanding labor costs in detail is essential for any organization looking to optimize its CNC machining operations. High labor costs can significantly impact the profitability of a project, making it critical to engage in detailed analysis and planning.
Skill Levels and Compensation
The skill level of personnel operating CNC machines is a vital determinant of labor costs. Skilled machinists can operate a CNC machine more efficiently due to their expertise and experience. As a result, they tend to command higher wages compared to less experienced workers. According to industry studies, skilled CNC operators can range from $20 to $40 per hour, depending on their qualifications and the complexity of the machinery they handle.
The investment in skilled labor can yield several benefits:
- Reduced Errors: Experienced operators make fewer mistakes, leading to less material wastage and lower overall costs.
- Faster Turnaround: Skilled workers often complete tasks more quickly, improving production timelines.
- Advanced Problem-Solving: Experienced machinists can diagnose issues in machine operations quickly, minimizing downtime.
Although higher wages for skilled labor can be a substantial upfront cost, the long-term savings from increased efficiency and reduced wastage often justify this investment.
Training and Development Costs
Investing in the training and development of CNC operators is an essential but often overlooked aspect of overall labor costs. Providing continuous education and skills training increases the capabilities of operators. Training programs can vary in media and structure, from formal classroom-based programs to hands-on workshops and even online courses.
There are various considerations to take into account when evaluating training costs:
- Initial Training: New hires often require substantial training, which can add initial costs that often go unaccounted.
- Continual Professional Development: Ongoing training is crucial to keep pace with technological advancements in CNC machining. This may come with additional costs.
- Return on Investment: While there are upfront costs associated with training, companies often see a return in the form of improved production efficiency and reduced error rates.
It is important to balance the costs and benefits of training. Organizations must determine which skills are most crucial and focus on developing competencies that align directly with production requirements.
Investing in labor costs is not just about hiring the right people, but also about ensuring they have the skills and knowledge necessary for effective CNC machining.
Maintenance and Operational Costs
Understanding maintenance and operational costs is vital in comprehending the overall CNC machining cost per hour. These costs significantly affect the profitability and efficiency of a manufacturing process. Every machine has operational requirements that include regular maintenance to function optimally. Without this, there can be considerable downtimes and inefficiencies. This not only impacts the bottom line, but also affects the overall productivity and reliability of the CNC operation.
Operations need to recognize that both routine and unscheduled maintenance play critical roles. Addressing these aspects effectively allows businesses to minimize interruptions in production. In turn, this aids in managing costs more efficiently.
Routine Maintenance Needs
Routine maintenance refers to scheduled interventions aimed at keeping CNC machines in proper working order. This includes tasks like lubrication, calibration, and software updates. Through a disciplined routine, one can prevent major breakdowns and enhance the life span of the equipment. Regular checks on precision and alignment also ensure that products meet quality standards.
Common components of routine maintenance include:
- Oil changes
- Filter replacements
- Tool sharpening
- System diagnostics
Regular maintenance helps in establishing a predictable cost structure. This can be integrated into the overall CNC operational budget. Investing efforts in preventive measures can reduce the likelihood of surprise repairs. Therefore, businesses should draft a maintenance schedule that outlines essential services, highlighting who is responsible for each task. This proactive approach can significantly lower cost per hour by minimizing machine downtime.
Unscheduled Repairs and Their Costs
Unscheduled repairs can prove to be a major headache for any manufacturing setup. These repairs often arise unexpectedly and can be caused by various factors, including wear and tear, equipment malfunction, or human error. When such situations occur, the costs can escalate rapidly.
Unscheduled repairs can result in extended downtimes, leading to lost revenue and increased operational costs.
The expenses related to unscheduled repairs consist of parts replacement, labor costs, and, importantly, the cost of lost production time. Companies can face different rates for emergency maintenance service depending on the severity of the malfunction and the availability of parts.
To address this issue, organizations need to track repair history meticulously. Analyzing data on past malfunctions can help identify recurring issues. This, in turn, aids in planning for future maintenance needs and averting unscheduled incidents.
Key strategies to mitigate unscheduled repairs include:
- Implementing predictive maintenance technologies
- Maintaining an inventory of critical spare parts
- Training staff to identify warning signs before breakdowns occur
Technological Advancements
Technological advancements in CNC machining are crucial for both operational efficiency and cost management. The integration of new technologies can significantly reduce time costs per hour. This not only influences production capabilities but also positions businesses competitively within the market. In this section, we will explore automation and software impacts, two key elements of technological advancement that can drastically reshape cost structures.
Automation in CNC Machining
Automation has transformed CNC machining landscapes. By reducing human involvement in repetitive tasks, automation lowers labor costs and minimizes human error. CNC machines equipped with automation can operate continuously, increasing productivity significantly. This leads to several benefits:
- Increased Output: Automated systems ensure higher production rates.
- Consistent Quality: Mechanized processes enhance uniformity in production, resulting in reduced waste.
- Lower Labor Costs: Companies can save substantially by reducing the number of operators required.
However, while automation offers these benefits, companies must also consider the initial investment for advanced automated systems. An analysis must be made to ensure that long-term savings justify the upfront capital.
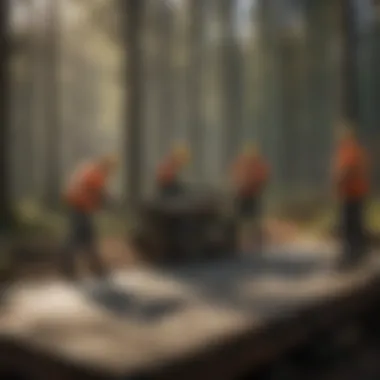
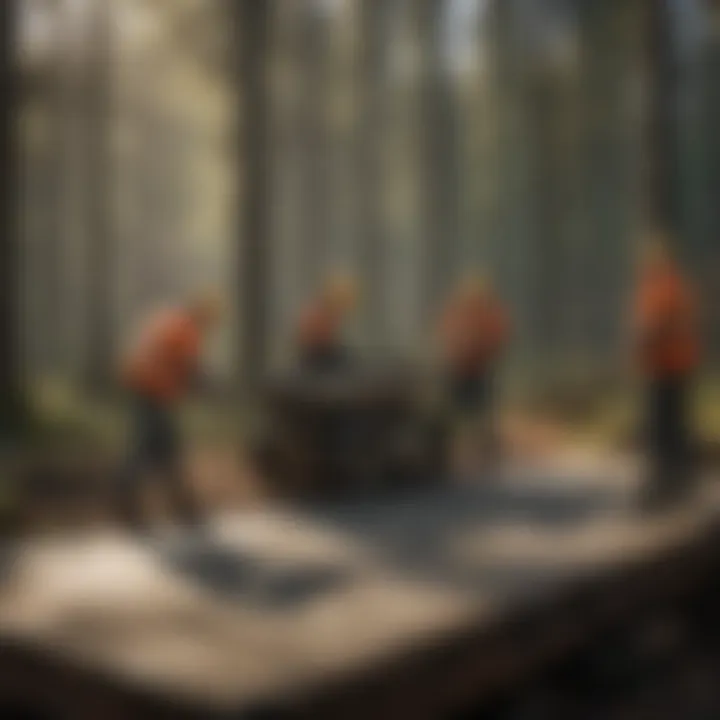
Software Impact on Costs
Software applications also play a significant role in managing CNC machining costs. Advanced software solutions enable better planning, real-time monitoring, and efficient resource allocation. Benefits include:
- Cost Estimation and Quoting: Programs that analyze materials, labor, and machine use help in precise quoting and planning.
- Scheduling Optimization: Software can help schedule production runs more effectively to reduce idle time and enhance output.
- Data Analytics: Using data collected from machine operations allows managers to identify inefficiencies and areas for improvement.
As companies adapt to new software, the cost implications need evaluation. Although some may see increased IT expenditures, the long-term gains in operational efficiency usually justify these investments.
Automation and software advancements are not just tools, they are pivotal strategies that can redefine cost structures in CNC machining.
Estimating CNC Machining Costs
Estimating the costs associated with CNC machining is a fundamental aspect for anyone involved in the manufacturing process. This estimation not only impacts the decision-making process but also influences budgeting and profitability. Accurate cost estimations allow companies to allocate resources efficiently and to understand which processes are economically viable.
Cost Calculation Methods
Calculating CNC machining costs involves various methods. Each method serves a purpose and provides a different perspective on the expenses involved.
- Hourly Rate Calculation: This common method focuses on the machine's operation time. The total cost is derived from the sum of direct costs per hour, including labor, machine depreciation, and associated overheads. By measuring the productive hours a machine runs, professionals can assess the effective hourly rate.
- Material Cost Analysis: Material selection dramatically affects overall costs. When predicting expenses, considering the price per unit of the material and the waste generated during machining is crucial. Materials like aluminum are often less expensive than titanium, for instance, leading to varying cost estimations based on the choices made.
- Time Studies: Detailed time studies help in determining cycle times and the overall productivity of the CNC process. These studies can reveal inefficiencies that contribute to higher costs. Data collected assists in refining cost projections and improving machining strategies.
- Cost-Volume-Profit Analysis: This method evaluates how cost changes impact profit. By understanding different operational volumes, companies can predict their breakeven points and profit margins, which is vital for long-term planning and scalability.
"A precise estimation of CNC machining costs transforms operational strategy and boosts competitive edge."
Real-World Examples
Understanding the theoretical aspects of cost estimation becomes even more enlightening through real-world examples.
- Example 1: A manufacturing firm switched from steel to a composite material, reducing their material costs significantly. Their estimation strategy included a detailed material cost analysis, which ultimately led to a 15% reduction in overall production costs.
- Example 2: A small business utilized time studies to evaluate the machining cycle times for their CNC routers. By identifying inefficiencies, they reduced cycle time by 20%. This reduction not only optimized labor costs but also improved throughput, which enhanced project delivery times.
Case Studies in CNC Cost Optimization
In the landscape of CNC machining, understanding cost optimization is crucial. Case studies delve into real-world applications, illustrating how businesses effectively manage and reduce their costs. These studies provide insights that cover a range of factors, such as material selection, machine efficiency, and workforce management. By examining these success stories, one can see the tangible benefits of strategic planning and precise execution. Moreover, they highlight the importance of continuous improvement, which is essential in a competitive market.
Success Stories from the Industry
Several companies have paved the way in exemplary cost optimization within CNC machining. For instance, a notable case involves a manufacturer who implemented automated systems. With newer technologies, they significantly reduced cycle times. The integration of robotics led to a decrease in labor costs and an increase in production speed.
Another compelling example is found within the aerospace sector. A company revamped its machine shop layout. They focused on reducing setup times, which directly influenced overall productivity. The results showed a reduction in downtime and increased throughput, allowing them to fulfill orders more rapidly and efficiently.
These success stories emphasize that a thoughtful approach to CNC machining can yield significant cost savings. The results are often tangible, driving both revenue and operational efficiency.
Lessons Learned
From these case studies, numerous lessons emerge that can guide future practices in CNC cost optimization. One primary takeaway is the necessity of investing in technology. The initial costs of automation or advanced machinery can be substantial but lead to long-term savings and increased productivity.
Another important lesson is the value of employee training. A skilled workforce is essential for maximizing the capabilities of CNC machines. Training programs can enhance skill levels, resulting in reduced errors and improved operational efficiency.
Additionally, maintaining open communication between departments can foster collaboration. This can lead to innovative problem-solving and the identification of areas needing improvement. The importance of a systematic review of processes cannot be overstated. Regular assessments of operational procedures often reveal opportunities for optimization that might not be initially apparent.
In summary, the use of case studies in CNC cost optimization reveals real-world applications of strategies that lead to success. The specifics underscore the importance of innovation and adaptability in a constantly evolving field like CNC machining. By learning from these experiences, companies can refine their approaches and build a more sustainable future.
Future Trends in CNC Costs
Understanding the future trends in CNC costs is crucial as the industry evolves. As manufacturers seek to improve efficiency and reduce expenses, many elements emerge that will dictate how costs will be structured moving forward. Factors like sustainability and emerging technologies play significant roles in shaping these trends, impacting everything from material selection to process optimization. A thorough grasp of these dynamics ensures businesses remain competitive and responsive to market changes.
Sustainability and Cost Implications
Sustainability is increasingly a focus for firms involved in CNC machining. Environmental concerns have prompted many manufacturers to reassess their operating procedures. The integration of sustainable practices not only affects the machinery used but also influences overall costs. This shift towards sustainability often leads to varying initial investments with long-term benefits.
- Reduction in Waste: Implementation of sustainable practices often results in less material waste, which directly correlates with lower material costs over time.
- Compliance Costs: Moving towards eco-friendly processes may incur upfront costs, particularly if new equipment or technologies are required. However, compliance with environmental regulations can avert larger fines and sustainability challenges.
- Energy Efficiency: Investing in energy-efficient machines can lead to substantial savings. Over time, the reduced utility costs can balance the initial high expenditures.
It is essential for businesses to weigh these sustainability implications. By prioritizing eco-friendly methods, companies can not only reduce their operational costs but also enhance their market standing among consumers looking for socially responsible products.
Emerging Technologies in CNC
The landscape of CNC machining is rapidly changing due to technological innovations. The advent of new technologies has significant implications for both efficiency and cost structures in the industry. Several notable trends have emerged:
- 3D Printing Integration: As additive manufacturing becomes more mainstream, it offers a complementary role to CNC machining. This will likely change cost bases by reducing the need for raw materials and enhancing production times.
- Advanced Software Solutions: Developments in software can optimize machining processes by improving scheduling and workflow, which helps in minimizing machine downtimes and labor costs.
- IoT and Real-Time Monitoring: The Internet of Things (IoT) enables machines to provide real-time feedback, allowing for proactive adjustments in operations and better predictive maintenance, ultimately aligning resources closely with production needs.
"Technological advancements will redefine CNC machining economics, making it essential for professionals to adapt quickly and efficiently."
These emerging technologies not only enhance operational efficiencies but can alter the financial landscape of CNC machining altogether. Adapting early can be beneficial for positioning within the market.
Understanding these future trends in CNC costs is important. It allows businesses to make informed decisions, ensuring they not only stay current but also thrive amidst evolving market demands.