Essential Insights on Trailer Inspection Sheets
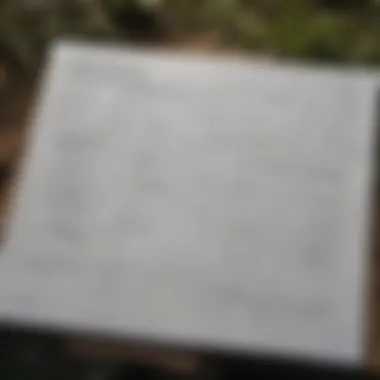

Intro
In the complex landscape of the transportation sector, ensuring the safety and efficiency of trailer operations is paramount. One effective tool that emerges in this context is the trailer inspection sheet. It serves as a formalized method to evaluate the condition and compliance of trailers before they hit the road. This article seeks to dissect the importance, processes, and implementation strategies associated with these inspection sheets, ultimately providing relevant knowledge to stakeholders.
Understanding that regular inspections can prevent accidents and enhance operational performance is critical for transportation professionals. The significance of trailer inspection sheets cannot be overstated; they not only aid in compliance with regulatory standards but also promote a culture of safety.
In the following sections, we will delve into the essential components of an effective inspection sheet, explore current regulatory requirements, and propose best practices for implementing robust inspection protocols.
Understanding Trailer Inspection Sheets
Understanding Trailer Inspection Sheets is crucial for ensuring safety and efficiency in the transportation sector. These documents serve as a systematic approach for evaluating the condition of trailers, providing a reliable method for identifying potential hazards and ensuring compliance with regulatory standards. Clearly defined inspection sheets help streamline the process of checking trailers, establishing a consistent protocol that enhances accountability among drivers and companies alike.
Definition and Purpose
A trailer inspection sheet is a detailed record that outlines the specific criteria to be assessed during the inspection of a trailer. This document typically includes various categories such as
- body condition,
- frame integrity,
- brake systems,
- lighting systems, and
- tire conditions.
The purpose of this sheet is to provide a comprehensive checklist for inspectors to follow, ensuring that no critical areas are overlooked during evaluations. By documenting inspections, businesses can maintain an accurate history of their trailers, aiding in both maintenance and compliance efforts.
Importance in Transportation
The importance of trailer inspection sheets in transportation cannot be overstated. They play a vital role in enhancing safety on the roads, ensuring that trailers are in good working condition before they are put into service. Without proper inspections, trailer-related incidents can lead to significant accidents, which can result in loss of life, injury, and substantial financial damage. Furthermore, these sheets help businesses adhere to regulatory compliance, as many jurisdictions mandate regular inspections of commercial vehicles. By following an established inspection process, companies can
- avoid fines,
- prevent vehicle breakdowns, and
- increase overall operational efficiency.
Regular inspections supported by proper documentation not only promote safety but also protect the company's reputation and financial stability.
In summary, understanding trailer inspection sheets aids stakeholders in maintaining high standards of safety and compliance. This foundational knowledge allows for better decision-making regarding fleet management and maintenance activities, contributing to the overall sustainability of operations.
Key Components of a Trailer Inspection Sheet
The components of a trailer inspection sheet are foundational to the safety and efficiency in the transport sector. Each part plays a crucial role in ensuring that trailers meet regulatory standards and are safe for operation. The key components encompass not just the physical elements of the trailer but also processes that ensure thorough documentation and compliance with regulations. Understanding these components is essential for stakeholders aiming to enhance their inspection processes.
Visual Inspection Criteria
Body Condition
The body condition of a trailer significantly influences its overall safety and functionality. Inspectors must examine the outer surface for any visible damage, rust, or structural weaknesses. A well-maintained body not only enhances aesthetic appeal but also contributes to aerodynamic efficiency.
The key characteristic of a sound body condition is the absence of corrosion. This factor makes the trailer less prone to premature wear. A sound body is beneficial because it usually indicates a lower risk of load shifting or structural failure during transit. On the downside, minor damages might go unnoticed if not inspected thoroughly, leading to more significant issues later.
Frame Integrity
Frame integrity forms the backbone of trailer safety. It ensures that the trailer can withstand the stresses of heavy loads and rough terrain. Inspectors pay close attention to cracks, signs of welding failure, or deformation. A robust frame is often synonymous with long-lasting service and reduced maintenance costs.
The significant aspect of frame integrity is its ability to support the trailer under various conditions. This characteristic is critical, as a compromised frame can lead to catastrophic failures. If flaws are found, immediate rectification is mandatory, as ignoring them poses serious risks. However, inspections can be time-intensive and require specialization.
Brake Systems
Brake systems are one of the most vital components of trailer safety. A thorough examination should include checks for pad wear, fluid levels, and overall system responsiveness. A reliable braking system can make the difference between safety and an accident.
The prominent feature of an effective brake system is responsive braking performance. This characteristic makes the brake system indispensable in ensuring safe stopping distances, essential for preventing collisions. However, brake system inspections can become complicated, especially with various technologies in use. Regular assessments are necessary to maintain optimal functionality.
Functional Tests
Lighting System Check
The lighting system check is crucial for nighttime and low-visibility operations. Inspectors validate all lights, including brake lights, turn signals, and marker lights. Proper lighting is essential for safe operation and compliance with road safety regulations.
Notably, the reliability of the lighting system is highlighted by its capacity to signal intentions to other road users. This quality significantly decreases the likelihood of accidents. In some cases, the lighting failures may not be easily detectable without systematic testing, emphasizing the need for rigorous inspections.

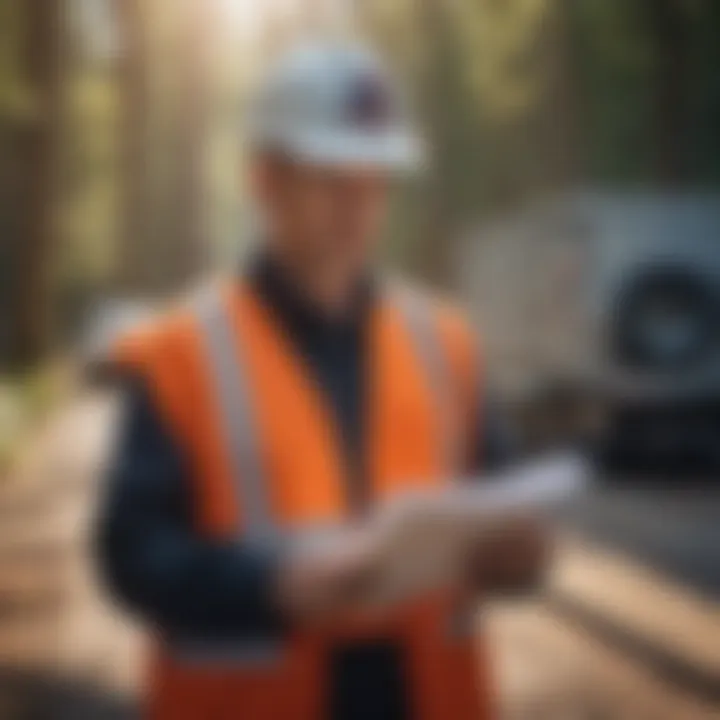
Wheel Bearings Assessment
Wheel bearings play a crucial role in maintaining wheel stability and performance. An assessment involving checking for play and grease levels can prevent wheel detachments while in motion. Regular checks can extend the lifespan of the trailer through proactive maintenance.
The critical characteristic of wheel bearing assessments is their ability to improve overall efficiency. Properly functioning bearings reduce resistance and improve fuel economy. Yet, maintaining wheel bearings requires specialized knowledge, and improper handling can lead to more severe issues.
Tire Readings
Tire readings are vital for ensuring optimal traction and loading capacity. Inspectors must check for tread depth, uneven wear, and air pressure. Accurate readings help in planning required maintenance and ensuring compliance with safety standards.
The key point here is that properly inflated and well-maintained tires contribute directly to vehicle stability. This factor is crucial, especially during long journeys. On the other hand, discrepancies in tire conditions can quickly escalate into significant safety risks if not monitored closely.
Documentation and Compliance
Regulatory Requirements
Adhering to regulatory requirements is non-negotiable in the inspection process. Each region has specific laws governing trailer safety, which requires diligent adherence. Regularly updated documentation can provide clarity about compliance status and inspections performed.
A key characteristic of regulatory requirements is their influence on operational licenses. Compliance ensures that transport companies can function legally, minimizing the risk of penalties. However, understanding the shifting landscape of regulations may pose challenges for operators trying to stay informed.
Record Keeping
Accurate record keeping is essential in the trailer inspection process. Detailed logs help track maintenance history and reduce uncertainty during inspections. This practice supports effective management and enhances operational efficiency.
The unique aspect of record keeping is its role in building a comprehensive maintenance history. This characteristic serves both immediate and longitudinal operational learning. However, the rigour of documentation can feel burdensome, yet it ultimately safeguards against liability.
Audit Trails
An effective audit trail provides accountability in trailer inspections. It ensures that all procedures are recorded and retrievable for review by regulatory bodies. As such, it serves as a transparent mechanism for accountability.
The key point about audit trails is their ability to highlight procedural adherence. This process assures stakeholders that inspections are carried out correctly, enhancing trust. Despite their usefulness, establishing and maintaining effective audit trails can require dedicating resources, particularly in larger operations.
Regulatory Compliance and Standards
Regulatory compliance and standards are central to the effectiveness of trailer inspections. These regulations ensure that operational practices meet the required safety and performance benchmarks. The adherence to these standards not only promotes the safety of the vehicles but also enhances the accountability of transport companies. Understanding compliance on both federal and state levels helps firms mitigate risks associated with violations, which can lead to substantial penalties and potential accidents.
Moreover, complying with regulations reflects a commitment to high operational standards that can improve a company's reputation in the market. This commitment cultivates trust among clients and partners, potentially leading to increased business opportunities.
Federal Regulations Overview
Federal regulations set baseline requirements for maintaining and inspecting trailers. The Federal Motor Carrier Safety Administration (FMCSA) governs these standards, mandating periodic inspections and maintenance for commercial motor vehicles, including trailers. The regulatory framework not only defines inspection frequency but also specifies the criteria that must be evaluated during inspections.
A significant regulation is the Federal Motor Carrier Safety Regulations (FMCSRs), which stipulates that trailers must pass annual safety inspections. The inspection criteria include checks on brake systems, lighting, coupling devices, and frame integrity. Companies must ensure that their inspection sheets cover all these requisite areas in detail.
Failure to comply with federal regulations can result in heavy fines, vehicle seizure, or even criminal charges against responsible parties. Thus, having a robust database that aligns with federal requirements is crucial for any transportation company.
State Regulations Variations
While federal regulations provide a common framework, it is essential to recognize that state regulations can diverge significantly. Different states may have specific inspection requirements based on local hazards or conditions, leading to a varied compliance landscape.
For example, California has stringent emissions requirements that affect how trailers are maintained, while states like Texas may focus more on road conditions and safety features. Hence, transport companies are advised to stay informed about the regulations applicable in each state where they operate. This ensures not only compliance but also optimal safety and performance of trailers.
Key considerations for navigating state variations include:
- Regularly updating knowledge of specific state laws related to trailer inspections.
- Collaborating with local authorities for guidance.
- Tailoring inspection protocols to meet or exceed local requirements.
Industry Best Practices
Adopting industry best practices enhances compliance and boosts the effectiveness of inspection processes. These practices go beyond mere compliance; they cultivate a culture of safety and responsibility.
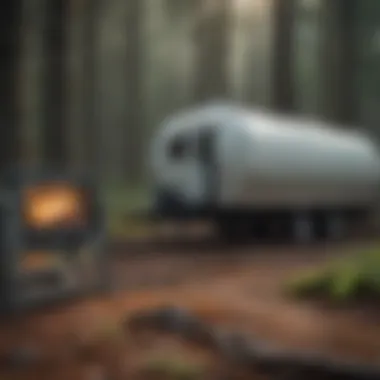
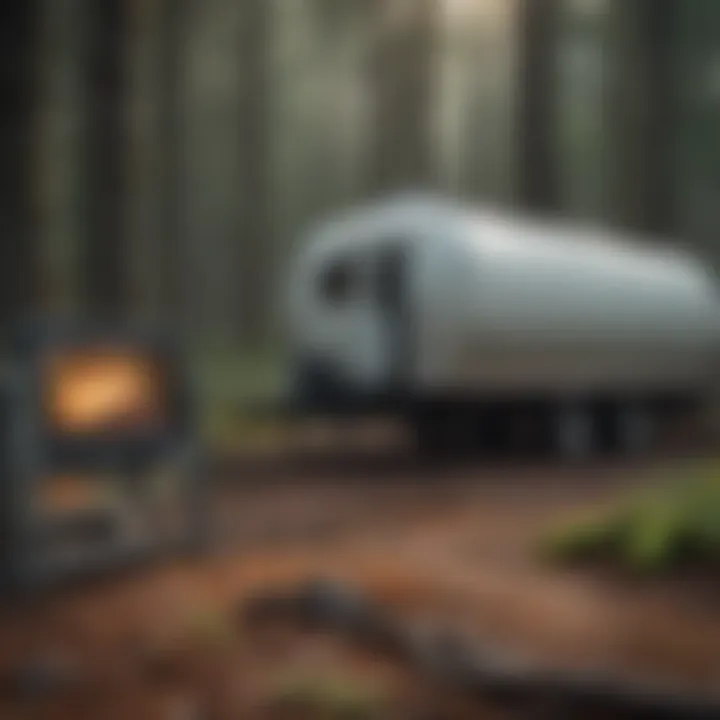
Some recommended best practices include:
- Conducting frequent training for inspectors to stay updated on compliance requirements and best inspection techniques.
- Utilizing digital tools for recording and tracking inspections, which can improve accuracy and accountability.
- Establishing regular audit schedules to evaluate internal inspection processes against both federal and state regulations.
Proper adherence to regulatory standards not only safeguards public safety but also protects the company's interests in the competitive landscape.
In summary, a structured approach to understanding and implementing both regulatory compliance and industry best practices is necessary for the effective management of trailer inspections. This proactive strategy can lead to better operational outcomes and enhance overall safety in transportation.
Implementing Effective Inspection Protocols
Implementing effective inspection protocols is vital in ensuring that trailer operations run smoothly and safely. A well-structured protocol can help identify potential problems before they escalate into costly repairs or unsafe conditions on the road. This section discusses key aspects of training personnel and utilizing technology as essential components to enhance the inspection process.
Training Personnel
Requirements for Inspectors
The qualifications and skills of inspectors play a crucial role in the success of trailer inspections. Inspectors must typically meet specific requirements that may include certifications, formal training, and practical experience. The focus on rigorous standards for inspectors not only enhances the credibility of inspections but also builds confidence in the industry.
One key characteristic of these requirements is their emphasis on understanding safety regulations and mechanical knowledge. This is beneficial as it ensures that inspectors are not just familiar with the inspection checklists, but also understand the implications of the findings on road safety. The unique feature of having certified inspectors is that it improves accountability. However, it can also create challenges for companies that need to invest time and resources in training.
Continuous Education
Continuous education is necessary to keep inspectors informed of the latest regulations, trends, and technologies. This aspect reinforces the idea that learning does not stop after initial training. By prioritizing continuous education, organizations can adapt to changes in safety standards and technological advancements.
The ongoing training programs highlight a key advantage: they equip inspectors with updated knowledge and skills. That is valuable in a rapidly changing regulatory environment. A distinguishing feature of continuous education is the flexibility it offers. Online courses and workshops often provide easy access to new information. On the downside, some companies may not prioritize continuous education, leading to skill gaps.
Utilizing Technology
Digital Inspection Tools
Digital inspection tools have transformed how inspections are conducted. These tools allow for precise data collection directly on-site. The implementation of digital formats aids inspectors in maintaining and organizing their records efficiently. This enhances the overall accountability of inspection processes.
A significant advantage of digital inspection tools is their ability to generate automatic reports. This feature minimizes errors associated with manual documentation, thus increasing accuracy. However, adopting digital tools requires upfront investment and training.
Mobile Applications
Mobile applications are also playing an increasingly important role in trailer inspections. They facilitate real-time reporting and communication between inspectors and fleet managers. This immediacy can lead to faster decision-making, as issues can be identified and addressed without delay.
A major characteristic of mobile applications is their user-friendliness, which is crucial for inspectors who may not be tech-savvy. A unique feature of these applications is that they can send notifications about upcoming inspections or deadlines. This helps maintain compliance. The downside, however, can be potential technical glitches, which may disrupt the inspection process.
"Effective inspection protocols lead not only to increased safety but also to improved operational efficiency across the transportation sector."
By focusing on these implementations, stakeholders can see improvements in safety, efficiency, and compliance in their trailer operations.
Challenges in Trailer Inspections
The process of trailer inspections is not without its complications. Understanding the challenges involved is essential for any stakeholder in the transportation sector. Challenges can arise from various aspects, such as human error, oversight in compliance, and limitations in technology. Awareness of these factors can greatly improve the inspection framework and enhance safety and compliance for all involved.
Common Pitfalls
Many issues can disrupt the effectiveness of trailer inspections. Some common pitfalls include inadequate training of inspection personnel. Inspectors not fully knowledgeable about regulations and standards may miss critical details.
Another common issue is the improper use of inspection sheets. When forms are partially filled or not updated, vital information might be overlooked, leading to unsafe operations.
Insufficient attention to detail is also a prevalent problem. Inspectors may focus on easily visible components while neglecting to conduct thorough evaluations of underlying mechanical systems. This oversight can lead to undetected issues before they escalate into serious problems.
Mitigating Risk Factors
To combat these challenges, proactive measures must be adopted. First, investing in comprehensive training programs for inspectors helps ensure they have the latest knowledge on regulations and inspection processes. Regular workshops can be beneficial in keeping staff informed.
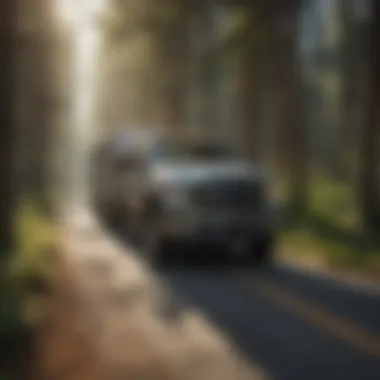
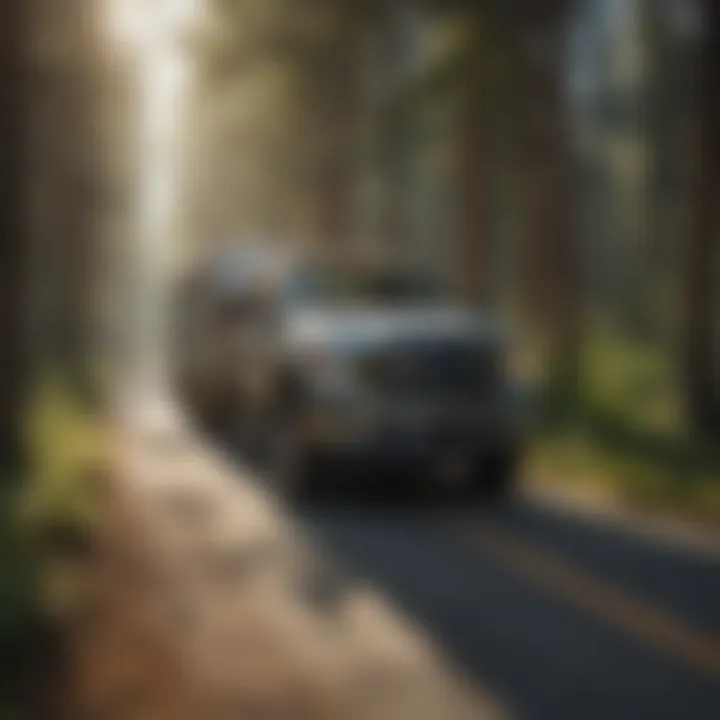
Adopting digital technologies can also streamline the inspection process. Mobile applications can aid inspectors in recording findings in real-time, reducing the chances of incomplete forms. These tools can also provide alerts for recurring issues based on past inspections.
Finally, creating a culture of accountability within the organization can minimize errors. Rewarding teams for thorough inspections and celebrating adherence to compliance standards can greatly improve performance.
"Effective trailer inspections require diligence, awareness of potential pitfalls, and a commitment to continuous improvement."
By tackling these challenges head-on, transportation stakeholders can achieve a higher standard of operational efficiency and safety.
Future Trends in Trailer Inspection
The evolution of trailer inspections is integral to enhancing safety and compliance within the transportation sector. Future trends center around technology and policy adaptations, which ultimately serve to improve the quality and accuracy of inspections. As the demand for efficiency grows, so does the need for inspections that are not only thorough but also timely. This section examines technological advancements and policy developments shaping the future of trailer inspections.
Technological Advancements
Automation Prospects
Automation is emerging as a significant trend in trailer inspections. The integration of automated systems simplifies various processes, from data collection to reporting. One of the key characteristics of automation is its ability to minimize human error. This not only increases accuracy but also enhances efficiency in identifying potential issues before they escalate. A unique feature of automation prospects is the real-time processing of data. This allows for immediate feedback and corrective actions, thereby reducing downtime. However, some concerns regarding the initial investment costs and the need for training workforce may pose challenges.
Advanced Diagnostics
Advanced diagnostics represent another critical facet of technological advancement in trailer inspections. This approach leverages sophisticated tools to assess the mechanical condition of trailers. A notable characteristic of advanced diagnostics is its capacity for predictive maintenance. By analyzing data trends, potential failures can be identified before they occur. This proactive strategy serves as a beneficial element in maintaining operational standards. However, there can be drawbacks like dependency on technology and possible technical malfunctions that could delay inspections if not managed correctly.
Policy Developments
Emerging Regulations
Emerging regulations play a crucial role in shaping the short-term and long-term goals of trailer inspections. The evolution of these regulatory frameworks ensures that safety protocols remain robust amid changing industry dynamics. A significant aspect of emerging regulations is their adaptability. As new risks and challenges are identified, these regulations can adjust, ensuring ongoing compliance. A unique feature of these emerging regulations is their potential to harmonize standards across different jurisdictions. Still, the continuous evolution can also create confusion for companies trying to keep abreast of compliance requirements.
Impacts on Industry Standards
The impacts on industry standards are notable as regulations evolve. These changes can enhance safety, improve compliance, and foster a culture of accountability within the transportation industry. A key characteristic is the push for higher qualification standards for inspectors and stringent evaluation criteria for trailers. This trend towards higher standards can lead to improved inspection quality. However, it may also increase operational costs as companies may need to invest in more comprehensive training and tools to meet expectations.
"Continuous evolution in regulations will enhance overall compliance but requires nuanced understanding from all stakeholders involved."
In summary, the future trends in trailer inspections reflect a dynamic interplay of technology and policy. Automation and advanced diagnostics present opportunities for improved efficiency and safety. Meanwhile, emerging regulations and their impacts on industry standards indicate a shift towards greater accountability in transportation. By understanding these trends, stakeholders can better prepare for the changes ahead.
The Role of Stakeholders
In the realm of trailer inspections, stakeholders are critical to ensuring the effectiveness of safety protocols and compliance measures. Each group involved in this process has its own set of responsibilities and motivations, and their collaboration is essential. Understanding these roles enhances the overall quality of the inspection process while also establishing a culture of safety within the transportation industry.
Transport Companies' Responsibilities
Transport companies bear the primary responsibility for implementing trailer inspection protocols. They must ensure that all vehicles in their fleet are regularly inspected and maintained. Failure to meet inspection standards can lead to significant legal ramifications and safety hazards.
Companies should establish a clear inspection schedule and designate trained personnel to perform assessments. Their responsibilities include:
- Conducting Regular Inspections: Systematically checking trailers for defects, ensuring compliance with regulations.
- Maintaining Records: Accurate record-keeping is vital. Each inspection should be documented thoroughly to provide evidence of compliance.
- Training Employees: All personnel involved in inspections must receive adequate training covering the latest regulations and inspection techniques.
Failure to adhere to these responsibilities can resonate throughout the industry. Not only does it pose risks to the companyโs reputation, but it also endangers public safety.
Regulatory Bodies' Oversight
Regulatory bodies play an essential role in the trailer inspection process by establishing guidelines and standards that transport companies must follow. Organizations such as the Federal Motor Carrier Safety Administration (FMCSA) in the United States set forth regulations that dictate how inspections should be conducted and what parameters must be met. These regulations serve several purposes:
- Facilitating Standardization: By providing uniform regulations, these bodies promote consistency in inspections across various transport companies.
- Enforcing Compliance: Regulatory bodies conduct audits and inspections to enforce compliance, ensuring companies adhere to established standards.
- Updating Standards: As technology and techniques evolve, regulatory bodies are responsible for updating inspection guidelines to reflect current best practices.
Stakeholders must understand that the oversight from regulatory bodies not only helps maintain safety standards but also encourages the transport industry to innovate in their inspection processes.
Fleet Management Implications
Effective fleet management must integrate robust trailer inspection protocols. Fleet managers need to approach inspections as a vital aspect of overall vehicle maintenance rather than merely a regulatory requirement. Their responsibilities include:
- Resource Allocation: Ensuring that the right tools and personnel are available for conducting thorough inspections is essential.
- Analyzing Data: Managers should closely examine inspection results to identify trends or recurring issues, leading to proactive maintenance strategies.
- Optimizing Operations: By integrating inspection data into operational planning, managers can improve efficiency, reduce downtime, and enhance safety.
Fleet management, therefore, not only impacts the safety of transport but also influences the financial performance of the company.
Overall, the collaboration between transport companies, regulatory bodies, and fleet management can significantly enhance the effectiveness of trailer inspections, leading to safer transportation practices and better compliance with regulations.