Building a Dry Kiln: Essential Techniques and Insights
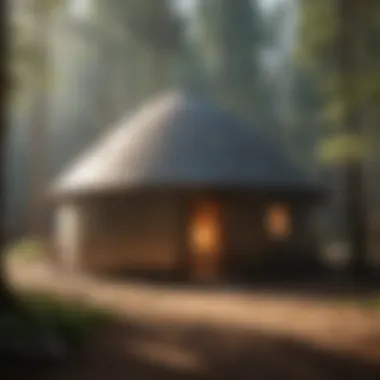
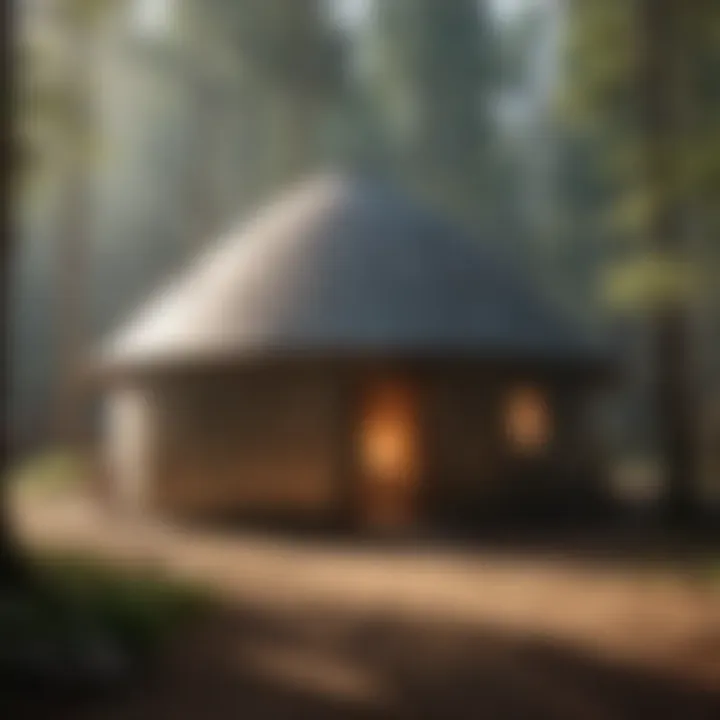
Intro
Creating a dry kiln is not merely an undertaking in woodworking; it's a practice deeply intertwined with the principles of sustainable forestry and effective resource management. For those in the lumber industry, understanding the nuances of dry kiln construction can significantly amplify both the quality of output and the efficiency of operations. In this guide, readers will explore the essential design principles, construction steps, and operational considerations that are crucial in this field.
The world of dry kilns goes beyond just drying out lumber; it touches on broader themes, such as maintaining the integrity of woodland ecosystems and implementing sustainable forestry techniques. Thus, it serves a dual purpose: facilitating efficient lumber processing while promoting environmental stewardship.
To understand this complex interplay, it's vital to first appreciate the role that forests play within our ecosystem.
Understanding Woodland Ecosystems
The health of our forests is critical, not only for biodiversity but also for the various ecological functions they serve.
Importance of Biodiversity in Forests
Diverse woodland ecosystems provide habitats for countless species, which in turn supports the intricate web of life that sustains our planet. Each tree, plant, and animal plays its part in nutrient cycling and energy flow within the ecosystem.
- Habitat Provision: Dense forests house various species of birds, insects, and mammals, which rely on different niches within these environments.
- Genetic Diversity: A vibrant array of plant species contributes to genetic resilience, enabling forests to adapt to changing conditions, such as climate shifts and disease resistance.
Role of Forests in Climate Regulation
Forests wield significant influence over climate regulation, primarily through the absorption of carbon dioxide. In fact, they act as natural carbon sinks, capturing and storing carbon, thus helping to mitigate climate change.
"Forestry management not only impacts wood production but also plays an essential role in climate stability."
Sustainable Forestry Practices
The intersection of dry kiln utilization and sustainable forestry is vital. Making informed choices about lumber processing can substantially benefit both the industry and the environment.
Principles of Sustainable Forestry
To be sustainable, forestry involves strategies that minimize ecological impact while enhancing forest resilience. Some key principles include:
- Selective Logging: Rather than clear-cutting, this method promotes the preservation of biodiversity by allowing some trees to remain, thus supporting habitat.
- Reforestation: Planting new trees to replace those harvested is essential for ensuring that forests endure.
Case Studies of Successful Implementations
Examining real-world applications illustrates the effectiveness of sustainable forestry practices. One noteworthy example is the use of dry kilns in small-scale sawmill operations. These operations often implement practices that conserve energy and reduce waste. By utilizing local species timber and processing it sustainably, they positively contribute to the ecosystem.
Incorporating a dry kiln into such operations not only enhances the quality of the dried product but also encourages responsible sourcing of materials.
Woodland Stewardship Techniques
Stewardship of woodland spaces encompasses more than just managing trees; it involves a holistic approach to maintaining healthy ecosystems.
Forest Management Plans
Creating a robust forest management plan is essential for any woodland owner aiming to balance productivity with conservation. These plans typically outline:
- Goals for Harvesting: Setting clear objectives for wood production while considering the health of the ecosystem.
- Monitoring and Assessment: Regularly tracking growth rates, health of trees, and the effects of forestry practices.
Conservation Strategies
Conservation in forestry can take on many forms, such as:
- Creating Wildlife Corridors: Ensuring that animals can migrate safely between habitats helps maintain biodiversity.
- Protecting Riparian Zones: Safeguarding these areas can prevent soil erosion and protect water quality by reducing runoff from logged areas.
As we delve deeper into the intricacies of building a dry kiln, keeping these principles and practices in mind will ensure that construction aligns seamlessly with sustainable forestry goals. Understanding how our actions contribute to larger ecological systems creates a foundation for responsible and informed choices in the field.
Foreword to Dry Kilns
In the world of forestry, the drying of wood is not just an afterthought; it's a vital process that can determine the quality and longevity of wood products. The introduction of dry kilns simplified and expedited the drying process, transforming traditional methods into a more controlled and efficient practice. Through this section, we will explore the foundational concepts of dry kilns, laying the groundwork for a comprehensive understanding of their importance and operation in lumber processing.
Defining Dry Kilns
A dry kiln might sound complex, but at its core, it's a specialized structure designed for reducing moisture content in freshly cut timber. Think of it as a controlled environment where conditions such as temperature, humidity, and air circulation are carefully monitored. Generally, dry kilns can vary in size, from smaller units suitable for hobbyist woodworkers to vast commercial setups used by large manufacturers.
The key characteristics of a dry kiln include:
- Temperature control: Allows for the effective evaporation of moisture.
- Ventilation systems: Ensures proper air circulation throughout the chamber.
- Humidity management: Helps maintain optimal conditions for wood drying without introducing defects.
Understanding what a dry kiln is sets the stage for grasping its broader applications within the industry. It's not merely about drying wood; it’s about optimizing quality and promoting sustainability in lumber production.
The Importance of Drying Wood
Wood, when initially harvested, contains an excess of moisture, which can lead to various problems if left untreated. The significance of drying wood goes beyond achieving the desired aesthetic; it deeply affects the wood's performance and durability.
Some of the key reasons why drying wood is crucial include:
- Preventing warping and cracking: Moisture causes wood to swell and shrink as temperatures change. Proper drying minimizes these shifts.
- Improving strength: Dried wood reaches its optimal strength properties, making it suitable for construction and furniture-making.
- Reducing biological risks: High moisture content creates an environment ripe for fungi and insects.
- Enhancing workability: Dried wood is easier to cut, shape, and finish, facilitating a smoother working experience for craftsmen.
The right moisture level in wood becomes paramount when it’s intended for specific applications, from cabinetry to heavy structural uses. Ultimately, drying wood isn't just a process—it's an art that ensures timber meets industry standards, and it’s an art richly enhanced by the technology of dry kilns.
"Drying wood not only enhances its usability but also prolongs its life, making it a cornerstone of forestry practices."
Thus, this introductory section has highlighted the pivotal role that dry kilns play in the drying process, intertwining the importance of defining these structures with their practical implications. As we continue, we will delve deeper into the types of dry kilns available, each with unique designs tailored to different drying needs.
Types of Dry Kilns
Understanding the types of dry kilns is essential for anyone involved in lumber processing and woodworking. Each type of kiln has its unique set of benefits and limitations, affecting efficiency, quality of drying, and overall energy consumption. By delving into the distinctions among conventional, solar, and vacuum kilns, one can make an informed decision that aligns with their specific needs and operational context. The choice of kiln affects not just how moisture is removed from the wood, but also how the heat and air flow will impact the quality of the final product.
Conventional Kilns
Conventional kilns, often referred to as forced-air kilns, can be found at many lumber operations. These structures utilize a heating system, typically powered by gas, electric, or wood, along with a system of fans to control airflow. The main advantage of conventional kilns is their capability to dry wood quickly, often within days rather than weeks. They offer a high degree of control over temperature and humidity, making it easier to tailor conditions to specific types of wood.
However, there’s a flip side. The fuel costs can add up, especially in colder climates where heating needs are more pronounced. Additionally, improper management of the drying process can lead to cracking or warping of the wood, diminishing its quality. Due to these factors, operators of conventional kilns must remain vigilant, constantly monitoring conditions to ensure optimal drying.
"The right drying technique can mean the difference between a high-quality lumber product and mere firewood."
Solar Kilns
Solar kilns harness the power of the sun, utilizing clear panels that trap heat while allowing humidity to escape. They represent an eco-friendly alternative to conventional systems, especially beneficial in regions with ample sunlight. The initial setup can be simple, often involving local materials and lower operational costs. Solar kilns tend to have lower energy costs than their conventional counterparts, which translates to cost savings in the long run.
However, these systems come with their own challenges. The drying process takes longer, sometimes stretching over several weeks. This slower pace can be a disadvantage for operations that require quick turnaround times. Therefore, solar kilns are best suited for smaller operations or those looking to minimize their carbon footprint. They demand attention to detail; as fluctuations in sunlight can drastically affect drying schedules.

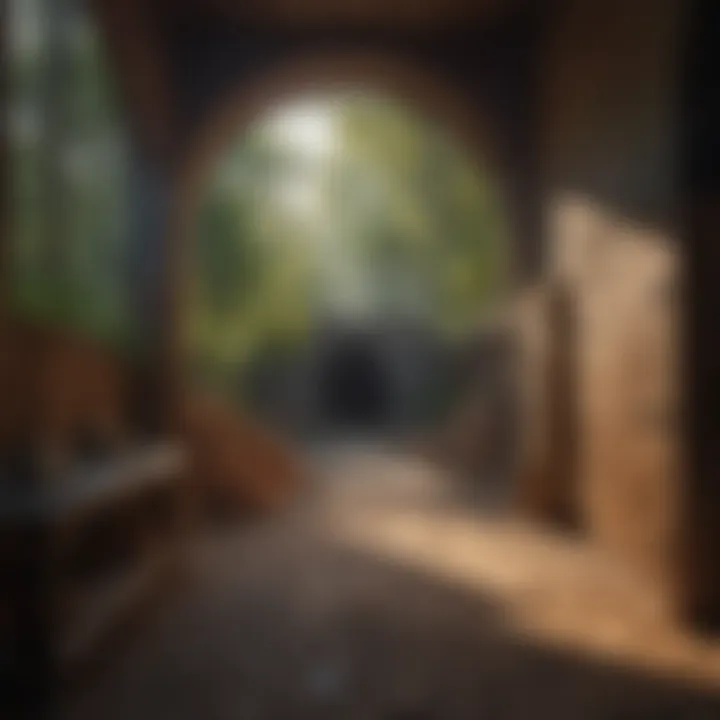
Vacuum Kilns
Vacuum kilns operate on a different principle altogether. By reducing the atmospheric pressure inside the chamber, these kilns lower the boiling point of water, allowing for very rapid moisture removal from the wood. This method is particularly effective for thicker pieces of lumber that conventional methods might struggle to dry without incurring damage.
The primary plus of vacuum kilns is their speed—they can achieve similar results in a fraction of the time compared to conventional systems. Additionally, they are less prone to defects like checking and warping due to the lower drying temperatures involved. But it's not all sunshine and rainbows; vacuum kilns can be costly, requiring significant investment upfront for both equipment and energy.
In summary, selecting the right type of dry kiln hinges on a variety of factors including cost, drying speed, available resources, and desired lumber quality. Each option brings its own pros and cons to the table, making it imperative for lumber operators to evaluate their specific needs before diving into construction or purchasing decisions.
Basic Principles of Kiln Drying
Understanding the basic principles of kiln drying is paramount for anyone venturing into the woodworking or forestry industry. It’s not just about chopping down trees and making furniture; it’s about sustaining quality and ensuring durability in the lumber. Proper drying methods can mean the difference between robust wood that stands the test of time and warped lumber that cracks under pressure. It’s through these principles that one can achieve the desired moisture content, which ultimately enhances the wood’s performance.
Understanding Humidity Control
Humidity control is like tuning an instrument; it’s crucial to get it just right. When drying wood, the air moisture level can drastically influence the drying rate. If the humidity in the kiln is too high, the wood will retain moisture, leading to problems like mold growth or decay. Conversely, if the humidity is too low, you risk over-drying, which can cause splitting or cracking.
To illustrate, consider how different wood species respond to humidity. Pine might tolerate a wider range of moisture levels compared to oak, which can be picky. Therefore, employing hygrometers and dehumidifiers within the kiln ensures that the environment remains stable and conducive for drying.
"Controlling humidity is half the battle won in kiln drying".
This underscores that knowing your material is as essential as controlling the environment.
Heat Transfer Mechanisms
Heat transfer in a kiln is fundamental to efficient drying. Heat moves from the heating source through the air and into the wood. Understanding how this process works can enhance your kiln's effectiveness. The basic mechanisms include conduction, convection, and radiation.
- Conduction happens when heat travels through solid mediums, like the walls of the kiln.
- Convection involves the movement of warm air around the wood, lifting moisture away.
- Radiation, though less common in kilns, can come into play if infrared heaters are used.
The temperature distribution within a kiln should be monitored closely. An uneven heat distribution can lead to inconsistent drying, causing some lumber to end up under-dried while others become over-dried. It’s advisable to invest in a good quality thermal imaging tool to visualize heat zones and make adjustments when necessary.
Moisture Content Reduction
Moisture content reduction is at the core of kiln drying. This process involves extracting moisture from the wood until it reaches the desired level, usually between 6%-12%, depending on the end use. It’s not as simple as flipping a switch and hoping for the best.
Understanding the wood species, thickness, and initial moisture content all play roles in determining the drying schedule. A rule of thumb is that thicker lumber takes longer to dry. By employing a gradual drying process—often referred to as a schedule—you can significantly improve the quality of the dried wood.
- Initial Phase: Start with a low temperature to avoid stressing the wood.
- Drying Phase: Gradually increase the temperature, keeping a watchful eye on moisture readings.
- Equalizing Phase: Once near target moisture levels, equalize the moisture throughout the stack to prevent internal stresses.
Controlling these phases through tailored schedules helps in achieving consistent results while reducing the risk of defects, making this a vital principle in kiln operations.
Planning Your Dry Kiln
Planning a dry kiln is a crucial step in the construction process. This phase sets the stage for the entire operation, ensuring that you’re well-prepared and that the structure meets all functional requirements. A well-thought-out plan not only saves time and resources later on but also enhances efficiency in the lumber drying process itself. Let’s take a closer look at the specific elements that need consideration in this planning phase.
Selecting a Suitable Location
Location isn’t just about picking a pretty spot; it’s a fundamental aspect of kiln efficiency and functionality. The chosen site should ideally be close to the lumber source to minimize transport time and costs. Hills or elevated areas can help with natural air movement, which can play a role in the drying process.
Here are some factors to weigh when selecting the location:
- Access to Utilities: Ensure easy access to electrical power and water, as these are often essential for kiln operation.
- Ground Stability: The site should be stable enough to support the heavy structure and avoid unexpected shifts, which could compromise its integrity.
- Environmental Conditions: Consider the local climate. Moderate temperatures and humidity levels can greatly impact the drying process. Extreme conditions may require more robust designs or additional equipment.
Design Considerations
A blueprint for your dry kiln shouldn't be drawn on a whim; instead, it requires careful thought. Various design considerations will impact how well your kiln performs. Design can influence airflow, heat distribution, and even energy efficiency.
Here are some core design aspects to think about:
- Size and Shape: The dimensions should accommodate the type and amount of lumber you plan to dry. A taller structure might allow for better airflow but can be trickier to manage.
- Material Choices: Use weather-resistant materials that can endure the rigors of kiln operations. High-density insulation can improve energy efficiency by keeping the heat where you want it.
- Airflow Mechanisms: Plan for optimal airflow. Ideally, air should circulate freely without creating dead zones where moisture can accumulate.
Capacity Planning
Capacity planning goes hand in hand with the type of lumber you are processing and the intended production output. An improperly sized kiln, either too big or too small, can lead to inefficiencies that cost both time and money in the long run.
When figuring out capacity:
- Assess your Drying Needs: Analyze the volume of lumber you usually dry in a season. This assessment should also consider scheduling variations and peak periods.
- Consider Batch Drying vs. Continuous Drying: Each method has unique capacity needs. For instance, batch drying may require a smaller unit, while continuous drying will need more room and complicated systems.
- Flexibility for Future Growth: Design with future needs in mind. If business grows, will your kiln be able to keep pace without needing a complete overhaul?
A well-thought-out plan can mean the difference between a smoothly running operation and a constant string of headaches and repairs.
In wrapping up this section, planning your dry kiln is a multifaceted endeavor requiring careful consideration of location, design, and capacity. Each element ties in deeply with operational effectiveness and overall productivity. Managing these variables well not only improves your processes but strengthens your position within the bustling market of lumber and forestry.
Materials Required for Construction
In the realm of dry kiln construction, selecting the right materials is like laying a solid foundation for a house. The choice of materials not only influences the kiln's efficiency but also impacts the quality of lumber produced. By carefully evaluating each component, builders can ensure that their kiln operates smoothly and effectively, adapting to the challenges of wood drying.
Structural Components
Structural integrity forms the backbone of any dry kiln design. The primary materials for constructing the frame typically include robust options like treated wood or metal. Using treated wood helps in resisting decay and pests, while metal components, like steel beams, can offer durability and stability under high temperatures.
A few key considerations when selecting structural components include:
- Load-Bearing Capacity: Ensure that the materials can handle the weight of the kiln’s contents and any additional factors, such as heat expansion.
- Moisture Resistance: Given the environment inside a dry kiln, moisture-resistant materials are preferable to prolong the structure's lifespan.
- Insulation Compatibility: The chosen materials should work well with the kiln's insulation system to minimize heat loss. Using a solid framework helps in keeping the ventilation system functioning effectively.
"The stronger the structure, the better the wood dries. Weak links produce weak results."
Insulation Materials
Insulation materials play a pivotal role in maintaining the desired temperature within a dry kiln. Without proper insulation, heat loss can become a major issue, leading to extended drying times and energy waste. Several insulation options exist, each with unique properties:
- Fiberglass: Lightweight and easy to install, fiberglass insulation is commonly used due to its effectiveness in controlling temperature.
- Spray Foam: With excellent sealing capabilities, spray foam can fill gaps and cracks that might allow heat to escape, improving energy efficiency significantly.
- Mineral Wool: This type is particularly resistant to fire, making it a safe choice for high-temperature environments.
When considering insulation materials, it's essential to balance cost with thermal performance. Investing in better insulation upfront can save on energy costs and enhance overall kiln performance down the road.
Heating Elements
Heating elements dictate the drying rate of the lumber, making their selection crucial to kiln operation. Different heating methods provide various advantages, depending on the style and design of the kiln:
- Electric Heaters: Ideal for smaller kilns, electric heating is controllable and precise, allowing for specific temperature settings.
- Hot Water Pipes: In larger setups, hot water pipes can effectively distribute heat throughout the kiln, offering consistent drying. This method works well with renewable energy sources.
- Wood-Fired Systems: For the rustic workshop, using wood-fired heating combines sustainability with traditional practices, but it requires careful management to ensure even heat distribution.
Step-by-Step Construction Process
The process of constructing a dry kiln is not just about putting together a structure; it involves a lot of planning, precision, and understanding the technical principles behind kiln drying. Each step plays a pivotal role in determining the efficiency and effectiveness of the kiln. By following a step-by-step approach, individuals can avoid common pitfalls, ensure optimal performance, and ultimately produce better quality lumber. This section will walk through every significant phase, from setting up the framework to the finer details that can make or break a project's success.

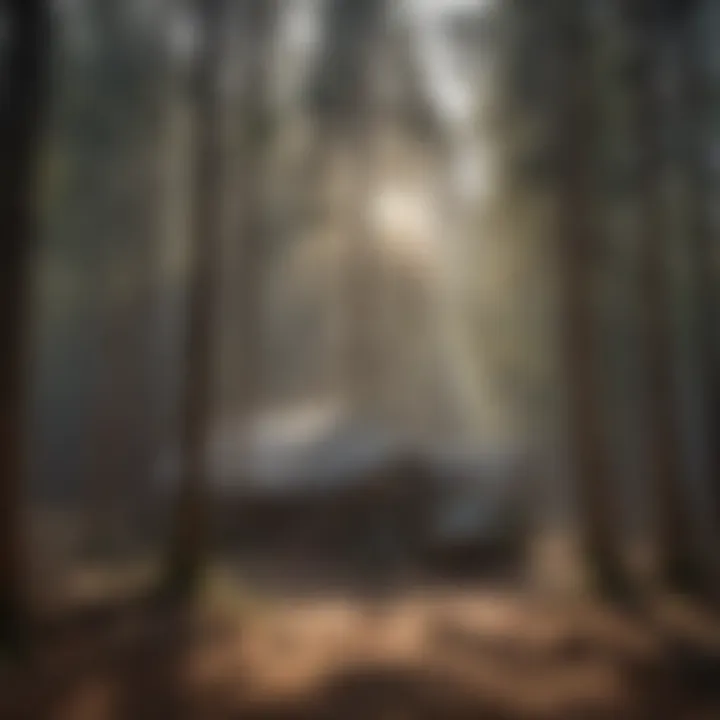
Building the Frame
Creating a solid frame is the backbone of a successful dry kiln. It must be sturdy enough to withstand both external pressures and the weight of the materials inside. Generally, wood is preferred for the framing due to its availability and workability, but steel can provide additional strength in larger kilns.
Key considerations include:
- Material Selection: When choosing wood, opt for a variety that has low moisture content to stave off warping or denting. Common choices might include treated lumber or certain types of hardwoods.
- Dimensions: Standard frame dimensions can be modified according to specific needs. Making the structure spacious allows better airflow, which is crucial for efficient drying.
To build the frame, start with the base using heavy timbers. Ensure the base is level before attaching vertical posts. Don't skimp on cross-bracing; this contributes significantly to stability.
Installing the Insulation
Insulation is paramount in achieving energy efficiency and maintaining consistent temperatures inside the kiln. Without proper insulation, heat will escape, leading to uneven drying and increased energy costs.
There are various methods to insulate a dry kiln. Some options include:
- Polystyrene Foam Boards: They offer an excellent insulation R-value, meaning they resist heat flow effectively.
- Fiberglass Batts: While somewhat easier to install, they may require a vapor barrier to prevent moisture build-up.
Tips for installation:
- Cover all interior walls thoroughly, ensuring that no gaps remain which could lead to heat loss.
- Pay attention to joints: This is where most air leakage occurs. Sealing materials with appropriate caulking can mitigate this issue.
Adding Heating Elements
Heating elements are what drive the drying process, thus selecting suitable types, such as electric resistance heaters or hot water pipes, is essential.
- Choosing heaters: Look for options that provide adjustable temperatures and fit your space without being too overbearing.
- Placement matters: Position the heating elements evenly throughout the kiln. You want the heat to distribute evenly to avoid hotspots and dry streaks in the lumber.
Connecting the heating elements to a thermostat allows precise control, helping maintain the necessary temperature range for optimal drying. This feature prevents overheating, which can damage wood quality.
Implementing Ventilation
Ventilation plays a crucial role in maintaining humidity levels within the kiln and ensuring consistent drying throughout the load. Without proper ventilation, moisture can become trapped, leading to conditions favorable to fungal growth or damage to the wood.
When setting up ventilation systems, consider the following:
- Placement of Vents: Ventilation should be strategically placed at both the high and low points of the kiln to create dynamic air circulation.
- Fans: Installing fans can help facilitate airflow, especially in larger kilns. A simple blower fan can work wonders in circulating warm air throughout the drying chamber.
Also, incorporating inlet and outlet vents with adjustable louvers allows for flexibility in managing airflow based on specific drying conditions.
Finishing Touches
Details matter; the finishing touches on a dry kiln enhance both functionality and aesthetics. This final phase shouldn't be ignored as it can improve operational effectiveness and longevity of the structure.
Important final steps include:
- Door Seal: Ensure that the entrance of the kiln seals properly. A well-sealed door prevents heat loss and draft.
- Control Panel Integration: Position a user-friendly control panel within easy reach to monitor and adjust conditions without hassle.
- Safety Features: Consider installing emergency shut-off switches, smoke detectors, and proper signage to enhance safety protocols.
In wrapping up the construction process, ensure that no tools are left inside the kiln, and perform checks to confirm everything operates as intended. A well-constructed kiln is an investment; treating it with care and attention during this phase can significantly pay dividends in the long run.
Operational Guidelines
Operational guidelines are the backbone of effective dry kiln management. Without them, it would be like sailing a ship without a compass. The guidelines in this section provide vital instructions and considerations for operating a dry kiln safely and efficiently. Understanding these topics empowers operators to maintain optimal conditions for wood drying, ensure lumber quality, and sustain healthy operating practices.
Monitoring Temperature and Humidity
Monitoring the temperature and humidity within a dry kiln is akin to keeping a pulse on the health of your project. Both factors are crucial in the drying process, influencing not just the speed of the drying, but also the quality of the finished product. If the temperature is too high, the moisture within the wood may evaporate too quickly, leading to cracks and defects. Conversely, if temperatures are too low, it can prolong drying unnecessarily, affecting the timber's usability and quality.
Key points to consider:
- Install reliable and precise thermometers and hygrometers throughout the kiln. This helps ensure you have accurate readings in real-time.
- Create a routine schedule to regularly check these readings and log them. Analyzing trends over time can provide insights into your drying process.
- Implement control systems that can automatically adjust conditions based on your measurements. This tech-savvy approach can help maintain a steady environment with minimal human intervention.
"A dry kiln with effective temperature and humidity monitoring is like a watchful guardian, protecting both the wood and the investment."
Adjusting Airflow Rates
Airflow in a dry kiln plays a crucial role in wood drying. Think of it as the winds that fill the sails of a ship, guiding it along its journey. Proper airflow ensures that moisture is effectively moved away from the wood. Insufficient airflow can result in uneven drying, while excessive airflow can lead to rapid surface drying, risking surface defects like checking or splitting.
To fine-tune airflow rates, consider:
- Ventilation openings: Ensure they are adjusted according to the specific wood species and dimensional factors. Different woods release moisture at varying rates.
- Use variable speed fans to tailor airflow precisely to meet the ongoing conditions within the kiln.
- Regularly check the airflow patterns. Ensure that there are no obstructions that could impede the air’s journey through the kiln.
Maintaining Optimal Conditions
Keeping optimal conditions is the final piece in the puzzle that is dry kiln operation. Just like a gardener tends to his plants, operators must nurture the kiln environment to flourish. Optimal conditions not only influence drying time but also overall wood quality post-drying. To maintain these conditions, operators need to juggle various components like temperature, humidity, airflow, and material loading effectively.
A few recommendations include:
- Regular calibration of all instruments to account for any drift in readings. This ensures that your measurements are always accurate.
- Perform routine maintenance checks on heating and ventilation systems. Any malfunction can throw your optimal conditions into disarray.
- Keep records of conditions and outcomes. Analyzing this data can help identify patterns that promote performance enhancements.
By adhering to these operational guidelines, it will be easier to achieve success in your kiln drying operations, resulting in higher quality lumber products and streamlined processes.
Quality Control in Drying
Quality control is a pivotal aspect of the drying process, particularly in the context of dry kilns. To ensure that lumber meets the required standards for performance and appearance, strict quality control measures must be implemented. This section will explore the significance of quality control, detailing the steps involved in assessing lumber, identifying defects, and rectifying any errors that may arise during the drying process.
Assessing Lumber Quality Post-Drying
After the drying process, it is paramount to assess the quality of the lumber. This evaluation not only highlights how effectively the drying process removed moisture but also the wood's condition following treatment. Key indicators to consider include:
- Moisture content levels: Using a moisture meter for accurate measurements ensures the lumber is within desired ranges suitable for its intended use.
- Visual inspection: Scrutinizing the surface for cracks, warping, or discoloration helps to pinpoint any anomalies that might affect usability.
- Stability tests: These assessments gauge bending or physical movement, providing insight into any potential long-term issues.
Regular assessments can catch issues early, preventing costly mistakes and ensuring the final product meets industry standards.
Identifying Defects
Defects in lumber can originate from numerous factors throughout the drying process. Identifying these defects early is crucial not just for quality assurance but to enhance customer satisfaction. Look out for:
- Checks and splits: Obvious signs of stress that can compromise structural integrity.
- Warping and twisting: These defects can occur from uneven drying, which hinder proper application in construction.
- Discoloration: Color changes sometimes indicate issues like mold or insect damage, both of which require immediate attention.
Maintaining a diligent eye during inspections can significantly reduce the risk of defects reaching the end user, highlighting the importance of extensive quality checks.
Rectifying Drying Errors
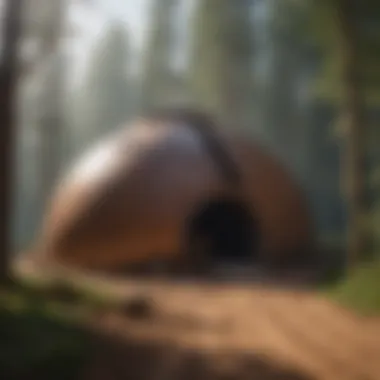
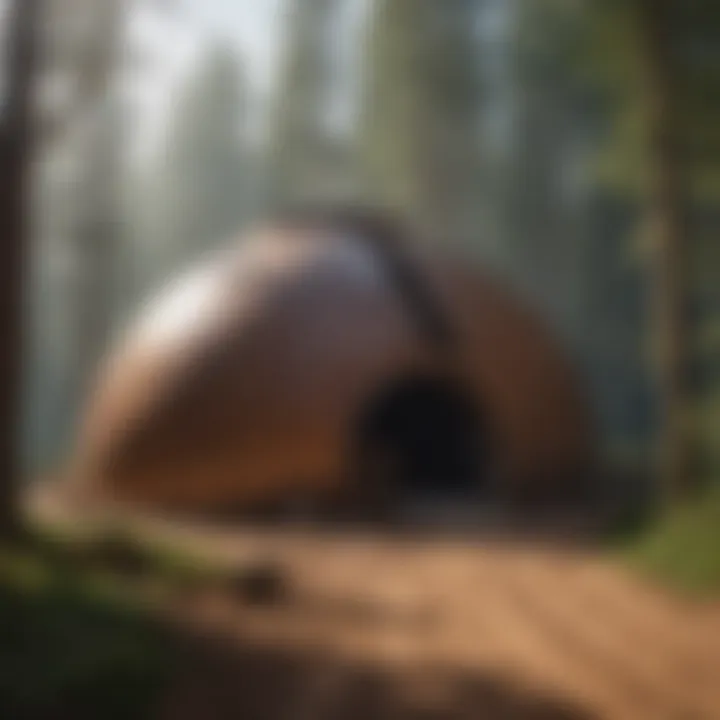
Even with the best intentions, errors can surface during the drying phase. Rectifying these errors not only improves the current batch but also informs future operations. Consider the following strategies:
- Adjust drying schedules: If there's evidence of overheating or too rapid drying, refining the schedule can help alleviate damage.
- Enhance airflow: Poor circulation can lead to localized humid conditions. Wifi-enabled fans or valves are an excellent modern solution to ensure even moisture evaporation.
- Retreat problem batches: Taking the time to redry questionable pieces can salvage potential losses. Assess these lumber pieces separately to implement a more tailored approach.
Ultimately, understanding the nuances of drying errors allows for a more refined drying process in subsequent runs.
"Quality control is not an option; it's a necessity. Each defect caught early is a victory toward excellence."
Safety Considerations
When constructing and operating a dry kiln, safety is not just a checkbox on a to-do list; it’s the foundation upon which your entire operation should stand. Ignoring safety precautions can lead to workplace accidents, damage to equipment, and potential threats to health that could ripple through any organization. It’s essential to consider these aspects not only to comply with regulations but to foster a culture of safety that benefits every individual involved in the process. Prioritizing safety means protecting your investments, your staff, and the integrity of your operations.
Operating Safely
Operating a dry kiln requires a thorough understanding of safety measures. To start, ensuring that all workers are familiar with their roles and responsibilities can significantly reduce risks. Training sessions, paired with hands-on demonstrations, can enhance knowledge about the equipment and potential hazards. Here are a few strategies that can help maintain a safe working environment:
- Wear Personal Protective Equipment (PPE): Always use appropriate protective gear—gloves, eye protection, and sturdy footwear should be standard fare.
- Regular Safety Drills: Practicing emergency scenarios prepares everyone for unexpected situations, making responses instinctive rather than hesitant.
- Maintain Clear Access: Ensure that pathways to exits and emergency equipment are unobstructed, reducing the chances of accidents during emergencies.
By creating a robust safety protocol and ensuring compliance, you provide a foundation that not only safeguards individuals but also enhances the overall operation of your dry kiln.
Handling Heat Sources
In a dry kiln, heat sources can pose serious risks if not handled with care. Various systems, like ambient heaters or steam generators, may be employed to maintain the required drying temperatures. Here are a few important considerations:
- Regular Inspections: Ensure that heat equipment is routinely checked for any signs of wear or malfunction.
- Temperature Monitoring: Implementing reliable temperature sensors helps in averting overheating, which can lead to potentially catastrophic failures.
- Proper Training on Equipment Usage: Workers must be trained to handle and operate heating devices correctly. A simple misunderstanding can lead to hazardous situations.
Remember: Always keep safety protocols in mind; neglect can lead not just to loss of material but to severe injuries.
Emergency Protocols
No matter how many precautions are taken, it’s vital to have emergency protocols in place. This ensures that in the unlikely event of an incident, everyone knows exactly what to do. Establishing clear protocols involves:
- Developing an Emergency Action Plan: This should outline every possible scenario from a fire to a sudden gas leak, including roles and responsibilities for each worker.
- Installing Emergency Equipment: Fire extinguishers, first aid kits, and emergency showers need to be accessible and frequently checked for functionality.
- Regular Training and Drills: Conducting routine training sessions will reinforce the importance of the protocols and ensure that staff feels equipped to deal with emergencies.
"Having a clear emergency protocol is like having a map in uncharted territory. It may not guarantee you won’t get lost, but it sure increases your chances of finding your way home safely."
By viewing safety not just as compliance but as an integral part of the daily routine, dry kiln operations can cultivate a safer workplace for everyone involved.
Environmental Impacts
The topic of environmental impacts in relation to dry kilns holds considerable importance, especially in today’s context where sustainability plays a pivotal role in forestry and lumber industries. Building and operating a dry kiln aren’t just about efficiency and output; these actions have a ripple effect on the surrounding ecosystem. Understanding the environmental implications is vital for both ethical practice and regulatory compliance. Notably, proper kiln design can reduce energy use and waste generation while enhancing wood quality through efficient moisture removal.
Sustainability in Kiln Operations
Sustainability isn’t merely a buzzword; it represents a shift towards practices that meet the needs of the present without jeopardizing future generations. This reliability can manifest in various ways, beginning with the choice of materials used in kiln construction. Opting for sustainably sourced wood or recycled materials not only minimizes environmental degradation but enhances the overall project’s credibility.
In terms of operations, adopting methods that reduce energy consumption can significantly contribute to sustainability. For example, when selecting a heating system for the kiln, one might consider options like biomass or solar heating, which can lower reliance on fossil fuels. Additionally, recycling waste heat from the drying process back into the kiln can slash energy costs further.
"By focusing on sustainability, we can improve our processes while taking better care of our planet."
Tools like moisture meters and programmable controllers can also be pivotal, as they help maintain optimum conditions while minimizing resource waste. Even small adjustments, such as adopting a staggered drying schedule that maximizes load capacity without compromising wood quality, can yield sizeable environmental benefits.
Minimizing Carbon Footprint
Minimizing carbon footprint is an essential aspect of modern kiln design. The carbon footprint of a dry kiln primarily stems from the energy consumed during the drying process. Reducing this consumption isn't just an operational goal but a necessary step toward ecological responsibility.
Implementing energy-efficient machinery is a straightforward approach. There are kilns in the market designed specifically with energy conservation in mind. Upgrading to these systems often makes a significant difference. Moreover, incorporating renewable energy sources, such as solar panels, can drastically cut down on carbon emissions associated with wood drying.
Adopting preventive maintenance practices is significant to ensure that kilns operate at peak efficiency, avoiding unnecessary energy wastage.
Here are several strategies on how to minimize your carbon footprint during kiln operations:
- Upgrade insulation to reduce heat loss, making the kiln more energy-efficient.
- Optimize airflow within the kiln to ensure even drying and reduce energy consumption.
- Use waste materials from the processing operation as fuel, thus recycling and reducing overall emissions.
Future Trends in Kiln Technology
As the demand for high-quality lumber continues to rise, the wood drying industry must evolve. Future trends in kiln technology reflect an intersection of innovation, sustainability, and efficiency. Understanding these trends is crucial for professionals who seek to remain competitive and effective in their operations. With advancements in materials and methods, there are several noteworthy developments poised to shape the future of dry kilns.
Emerging Innovations
The landscape of kiln technology is being reshaped by cutting-edge innovations that enhance drying processes. One of the most promising advancements is in sensor technologies. By means of moisture sensors, operators can get real-time readings that help in making immediate adjustments to conditions inside the kiln. This not only improves drying efficiency but also significantly reduces energy usage.
In addition, automation systems are increasingly making their way into kiln operation. Automated controls offer precise management of the drying environment, optimizing airflow and temperature for different types of wood. Furthermore, modular kilns are gaining traction. These units can be expanded or contracted based on production needs, making them highly flexible for operators.
- Advanced Monitoring: Integration of IoT technology allows for remote monitoring and control of kilns.
- Data-Driven Practices: Using big data analytics can help in predicting drying patterns and improving lumber quality.
- Cross-Laminated Timber Technology: New kiln designs specifically cater to this growing market, enabling faster and more efficient processing.
Integrating Energy Efficiency
Energy consumption has become an important focal point within kiln technology. As utility costs rise and environmental awareness grows, the quest to integrate energy efficiency into kiln designs takes center stage.
Firstly, incorporating insulated materials in kiln construction is essential. This minimizes heat loss, ensuring that the energy used for heating is effectively utilized. Likewise, the implementation of variable speed fans contributes to improved airflow rates while reducing energy consumption.
The utilization of renewable energy sources also stands out as a significant trend. Solar thermal collectors and biomass heating systems not only lower operational costs but also enhance sustainability. Some companies are harnessing biomass waste from other operations to heat their kilns, paving the way for energy-positive production cycles.
- Heat Recovery Systems: These systems reclaim and reuse heat that would otherwise be wasted.
- LED Lighting: Switching to energy-efficient lighting solutions can lower the energy consumption in kiln spaces, further reducing overall operational costs.
"In the realm of kiln technology, energy efficiency isn't merely a bonus; it's becoming a necessity."
As we look ahead, these innovations and trends aren't just about staying updated; they represent the next step towards optimizing kiln operations. Embracing these advancements will not only lead to cost savings but also contribute to the broader goals of sustainability and product quality in the woodworking industry.
End
The concluding section of an article about constructing a dry kiln serves as a pivotal anchor, tying all the discussed concepts together. It underscores the importance of effectively drying lumber, a critical step in ensuring the quality, durability, and appeal of wood products. As we’ve navigated through various aspects—ranging from foundational principles to specific designs—it becomes increasingly clear how each component interconnects in the journey of dry kiln construction and operation.
In particular, the environment inside a kiln dictates the success of the drying process. Understanding humidity control systems, the heat transfer mechanisms, and efficient moisture content reduction is not merely theoretical; these elements play a practical role in the outcomes seen in the timber industry. With optimal drying conditions, one can maximize yield and promote better quality lumber, which translates to higher market value.
"A well-constructed dry kiln stands as the backbone of any reputable woodworking operation; its effectiveness resonates through every piece of wood it treats."
Recap of Key Points
In wrapping up, let’s revisit the major elements highlighted throughout this article:
- Defining Dry Kilns: Understanding the purpose, operation, and various types, like conventional, solar, and vacuum kilns, sets the groundwork for choosing the right unit.
- Basic Principles of Drying: Discussing humidity control and heat transfer mechanics is essential for comprehending how to achieve optimal drying results.
- Construction Guidelines: Detailed insights into materials and step-by-step processes facilitate a clear path to building a dry kiln that meets specific operational needs.
- Operational and Safety Guidelines: Monitoring and ensuring safety minimizes risks while enhancing user confidence in their methods.
- Environmental Significance: The conversation around sustainability and minimizing the carbon footprint hones in on the broader impacts of kiln operation.
Encouragement for Practical Application
As we draw this discussion to a close, the invitation to practical application should resonate strongly with both experienced professionals and newcomers in the field. The principles laid out here are not mere concepts for academic discussion; they translate directly into real-world scenarios, influencing daily operations in woodworking facilities.
Setting a kiln in motion, managing its parameters, and reaping the benefits of properly dried lumber will set apart those who commit to the craft. Don’t shy away from experimenting with various designs tailored to your needs—whether it’s tweaking airflow for better humidity control or adjusting the materials for better insulation.
The beauty of constructing a dry kiln is in the learning that comes from action. Each project, regardless of size, provides vital experience that can push the boundaries of what's possible in wood drying. Embrace the nuances of the process; after all, practical application not only builds skill but fosters a deeper appreciation for the craftsmanship involved in lumber processing.